Talking with Stephan Friebel, Site Manager, Halle
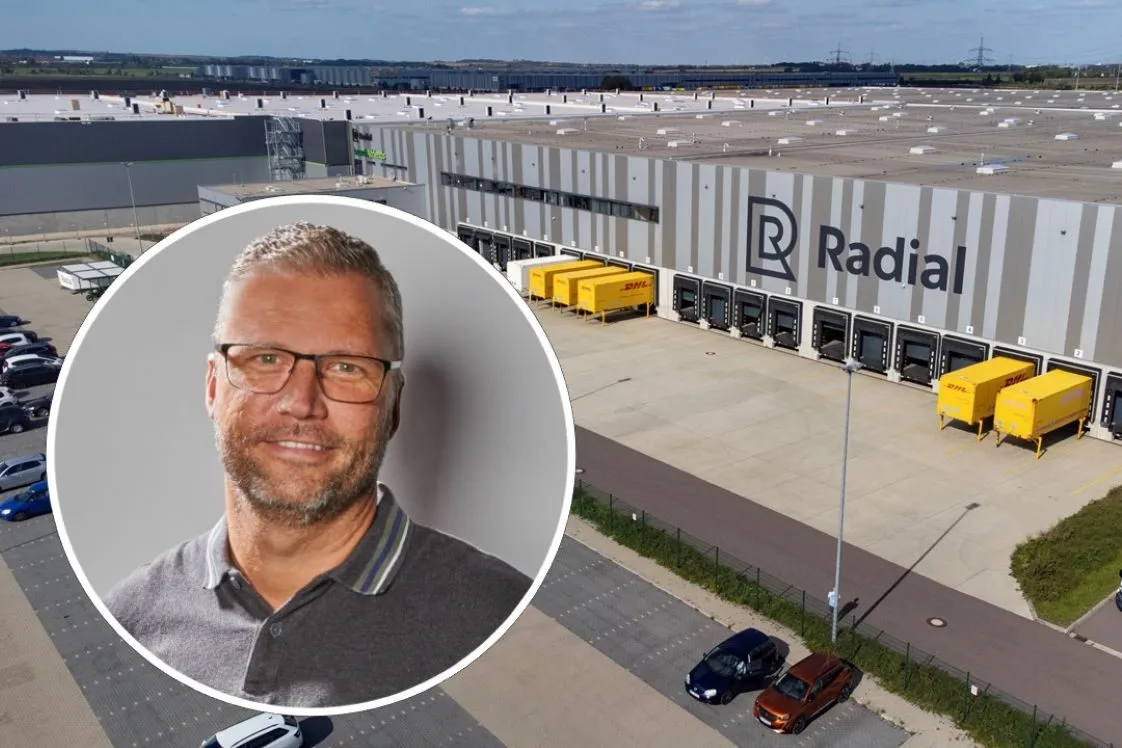
Explore the unique features of Radial’s facility as detailed by Stephan Friebel, the Site Manager in charge of operations in Halle, Germany.
Centrally located in Europe
Radial’s facility that you manage is strategically located. What are the benefits of this location?
Germany lies in the heart of Europe, and Halle is in the heart of Germany. We are very close to some of the biggest logistics hubs in Germany, such as DHL, Hermes, and DPD. These hubs are not more than 20 minutes away from us, which is a huge advantage when it comes to lead times for track carriers. The close proximity to national and international hubs makes late order cut-off times possible, which results in 24-hour deliveries across Germany and East Europe.
This proximity, along with our semi-automated warehouse, greatly enhances our efficiency.
55,000 square meters
What is the size of the fulfillment center in Halle?
We have a ground floor of 25,000 square meters, divided into three units, including a pick mezzanine. In total, with the pick mezzanine, we have 55,000 square meters of logistic floor space, with more than 300,000 bin locations.
This setup is ideal for ecommerce businesses like fashion, cosmetic, and jewelry.
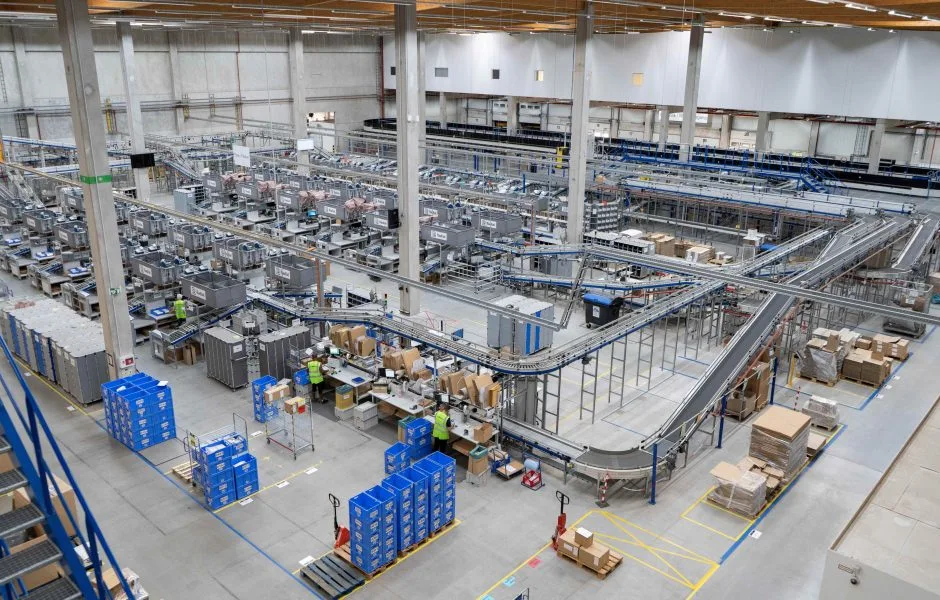
The conveyor system
Automated conveyor system
What investments were made to enhance the efficiency of this warehouse?
We offer a combination of manual and automated operations, reflecting our commitment to efficiency and productivity. In recent years, we’ve made significant investments, totaling several million euros, in our conveyor system.
Conveyor system streamlines our operations by allowing our staff to remain in their designated zones, efficiently handling articles by picking or putting them away and placing them on the conveyor. From there, items seamlessly progress to our sort-to-light system, where orders are promptly fulfilled and dispatched to the packing bench.
Our investment optimizes labour hours by minimizing movement across the warehouse, enhancing overall efficiency. This streamlined approach enables us to provide competitive pricing while upholding exceptional service standards for our clients.
3 shifts, 24/6
How do you manage workforce flexibility?
We currently have 170 employees operating on two shifts. However, we are flexible and can adjust based on volume. During peak times, we can extend to three shifts, working 24/6.
Due to the fluctuating nature of demand we cooperate with a local work agency. While we plan with forecasts, flexibility is crucial. I recommend maintaining a 10-15% core workforce completed with temporary workers.
This is particularly important because Mondays and Tuesdays are very busy with orders from the weekend, and by the end of the week, we aim to have all important stock ready for sale. Balancing the volume with agency workers helps manage this workload effectively.
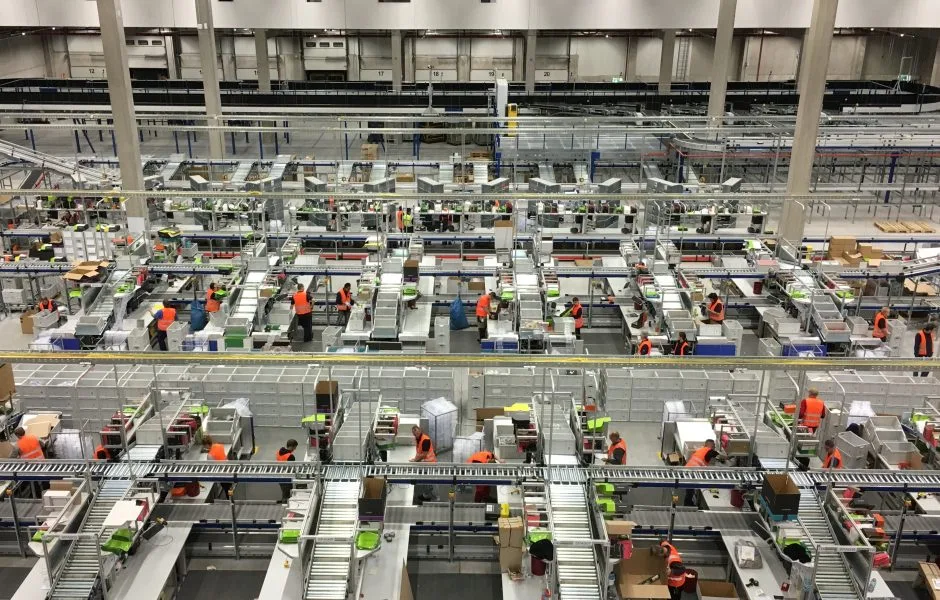
Packing area
Highly sustainable practices
What steps are you taking to reduce your ecological footprint?
Looking ahead, our goal is to become even more environmentally friendly. We are exploring various avenues, such as investing in solar panels.
Energy use is greatly minimized by implementing LED lighting across the facility. Moreover, motion and presence detection systems ensure that lights are only activated when needed in pick towers, common areas, and for conveyor belts.
We minimize packing with a “packaging on demand” system, recommend sustainable practices to our clients and encourage them to use 100% recyclable plastic, cartons made from grass, or other eco-friendly materials. We always emphasize the importance of transitioning now, as by 2030, plastic will not be allowed in the EU.
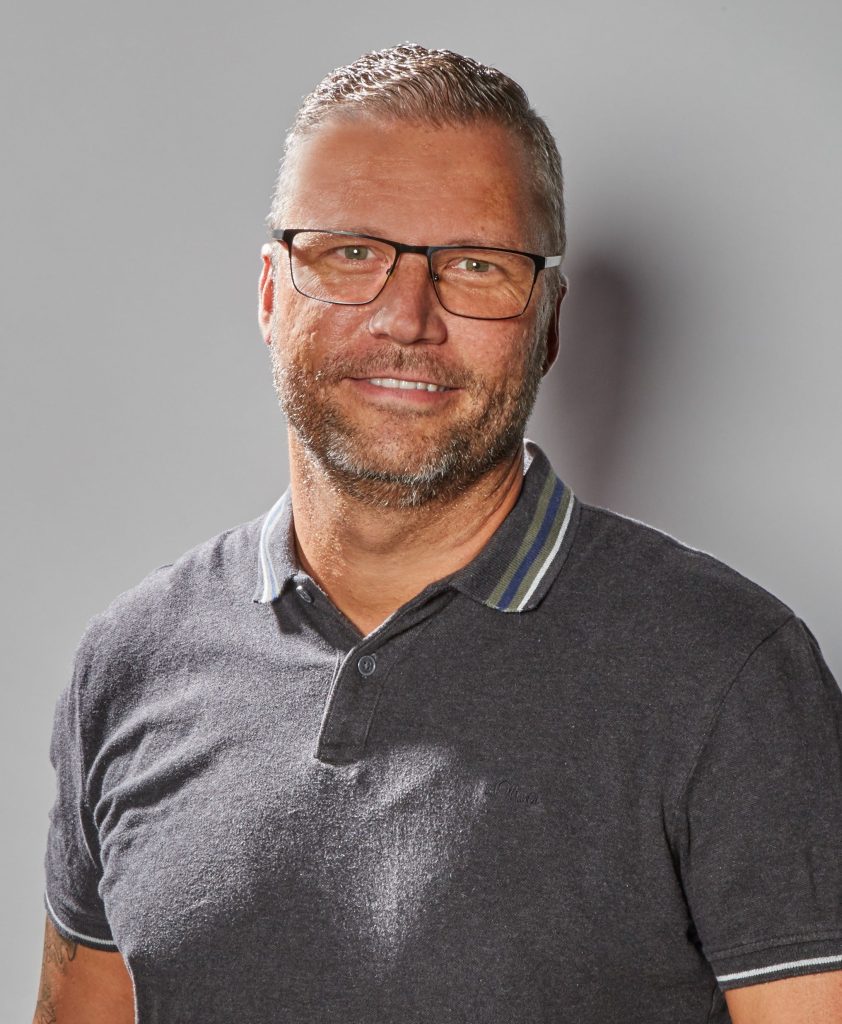
Stephan Friebel, Site Manager, Halle
Stephan is a logistics professional with 23 years of experience. He has seen logistics evolve from manual to highly automated operations and is at the forefront of driving efficiency and innovation in this field. Stephan’s achievements include launching a greenfield project in Germany for a globally renowned fashion ecommerce brand. He transformed an 80,000-square meter warehouse from manual to fully automated operations within two years. He enjoys working with people and excels in fostering teamwork and collaboration.
Looking for a fulfillment partner in Germany?