Mastering the Pick and Pack Process for Seamless Customer Experience
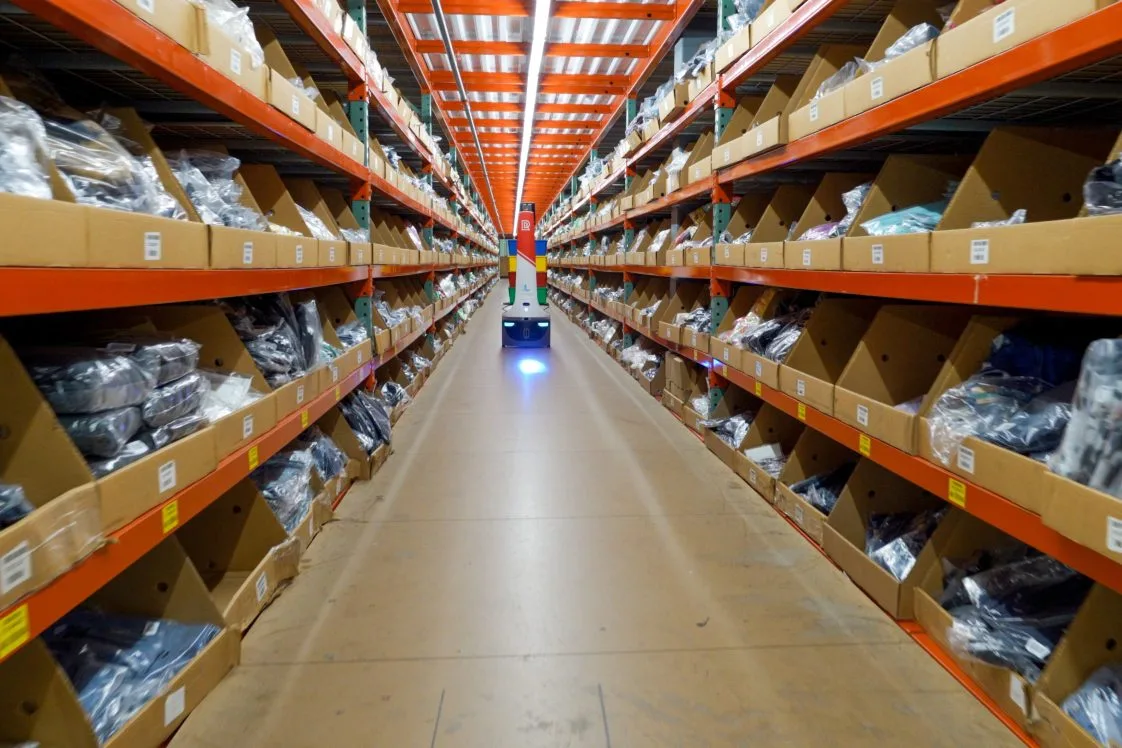
In today’s highly competitive marketplace, delivering seamless customer experiences is paramount for eCommerce fulfillment success. A crucial aspect of achieving this goal lies in mastering the pick and pack process, which directly impacts the speed, accuracy, and overall efficiency of order fulfillment.
This article explores the essential elements of pick and pack operations. Keep reading to learn more about how retailers can optimize their processes to create seamless customer experiences.
Understanding the Pick and Pack Process
Pick and pack is a warehousing process and critical step in order fulfillment in which warehouse workers select items from inventory and package them for shipment to customers. It plays a crucial role in ensuring accurate and efficient delivery and directly contributes to the overall customer experience and profitability.
Let’s take a closer look at the key stages and considerations involved in the pick and pack process.
- Order Retrieval: Pick and pack services begin with retrieving eCommerce orders from an order management system or database. This step involves accessing relevant order details, including product SKUs, quantities, shipping addresses, and any special instructions or customer preferences.
- Product Picking: Once the orders are retrieved, the next step is to locate the ordered items within the warehouse shelves or eCommerce fulfillment centers. Depending on the size and organization of the inventory, different picking methods may be employed, such as zone picking, batch picking, or wave picking. The goal is to efficiently gather the required items while minimizing time, effort, and costs.
- Quantity Verification: Accuracy is crucial during the pick and pack process. It is essential to verify that the correct quantity of each item is picked to fulfill the customer’s order accurately. This can be done through manual checks or by leveraging technology, such as barcode scanning systems, to ensure precision.
- Packaging: After picking the items, they must be appropriately packaged for safe transportation. Packaging materials, such as boxes, bubble wrap, or padding, are selected based on the nature and fragility of the products. Packaging should protect the items, optimize space utilization, and minimize any potential damage during transit.
- Labeling: Each package should be labeled accurately with the necessary shipping labels, barcodes, and any additional documentation required for proper handling and tracking. Clear and legible labeling is crucial for efficient warehouse operations and to ensure that the package reaches the correct destination without delays or errors.
- Quality Control: Before shipping orders, a quality control check is conducted to ensure the accuracy and condition of the picked items. This step involves inspecting the items for any defects, ensuring that the correct products are included, and verifying that the packing materials are secure and intact.
- Shipping and Documentation: Once the pick and pack process is complete and quality control checks are passed, the packages are ready for shipment. The appropriate shipping method is chosen based on customer preferences or predetermined logistics arrangements. Documentation, such as invoices, packing slips, or customs forms, may also be prepared and included as required.
Benefits of Streamlined Pick and Pack
A streamlined pick and pack process offers numerous benefits for online businesses in order fulfillment. By optimizing this crucial aspect of operations, companies can enhance their overall efficiency and customer satisfaction.
- Faster Order Processing: Streamlining the pick and pack process reduces the time taken to fulfill orders. Faster order processing enables businesses to meet tight delivery deadlines and offer quicker shipping options, leading to improved customer satisfaction and loyalty.
- Increased Accuracy: By minimizing manual handling and implementing technology such as barcode scanning and automation, a streamlined pick and pack process significantly reduces the likelihood of errors in order fulfillment. Accurate orders lead to fewer returns and exchanges, saving both time and money.
- Improved Warehouse Productivity: With a well-organized warehouse layout and efficient picking strategies, warehouse staff can work more productively. Optimized pick paths and batch picking methods minimize unnecessary movement, maximizing the number of orders processed per hour.
- Scalability and Growth: As businesses grow, a streamlined pick and pack process can adapt to higher order volumes and increased demand. The efficiency gained through optimization allows companies to handle larger order volumes without compromising on quality or customer experience.
- Ability to Offer More Fulfillment Options: A well-optimized pick and pack process allows businesses to offer a broader range of fulfillment options to customers, such as same-day or next-day delivery. This flexibility can give a competitive edge and attract more customers.
- Data-Driven Decision Making: Streamlined pick and pack processes often integrate with warehouse management systems (WMS) and other technologies, providing valuable data insights. Businesses can use this data to make informed decisions about inventory management, order fulfillment strategies, and overall process improvement.
Pick and Pack Strategies
There are several pick and pack methods that online stores can employ to optimize their order fulfillment processes. You can also outsource fulfillment services to have pick and pack warehouse processes performed for you.
Piece Picking
Piece picking, also known as individual picking or single-item picking, involves selecting and retrieving individual items or products from their storage locations in the warehouse.
In piece picking, each item is typically picked and packed separately according to specific customer orders or requirements. This strategy is commonly employed in e-commerce fulfillment centers or when dealing with small and diverse orders.
Zone Picking
In zone picking, the warehouse is divided into distinct zones, and each picker is assigned to a specific zone. Pickers are responsible for picking items only from their designated zones. Once the items are picked, they are consolidated at a central location for packing. Zone picking is effective for large warehouses with a wide range of products.
Batch Picking
Batch picking involves picking multiple orders simultaneously. Pickers are assigned a batch of orders that have common items. They move through the warehouse and collect the required items for all the orders in their batch. This method maximizes efficiency by reducing travel time and optimizing picking routes.
Wave Picking
Wave picking combines elements of both zone picking and batch picking. The warehouse is divided into zones, and pickers are assigned specific zones to work in. However, instead of picking one order at a time, pickers are assigned multiple orders that can be completed in a single wave. This method improves efficiency by optimizing picking routes within each zone.
Discrete Order Picking
Discrete order picking is a traditional method where each picker is responsible for picking items for a specific order. Pickers move through the warehouse, picking items one order at a time. This method ensures order accuracy but may result in more travel time compared to batch or wave picking methods.
Automated Picking Systems
Automation technologies, such as conveyors, robots, and automated storage and retrieval systems (AS/RS), can be used for efficient pick and pack processes. These systems use advanced technologies to automatically pick up and transport items to packing stations. They can significantly improve speed, accuracy, and overall efficiency in order fulfillment.
Best Practices for Optimizing the Pick and Pack Fulfillment Process
Optimizing the pick and pack process is essential for improving efficiency, accuracy, and overall customer satisfaction in order fulfillment. Here are some key strategies to optimize the pick and pack process:
- Efficient Warehouse Layout: Designing an organized and intuitive warehouse layout can significantly improve the pick and pack process. Ensure that popular and frequently picked items are easily accessible and strategically located near the packing area. This reduces travel time and minimizes the effort required to retrieve items.
- Inventory Management: Implement a robust inventory management system to maintain accurate stock levels and prevent stockouts or overstocking. Utilize inventory tracking systems and real-time inventory visibility to streamline the pick and pack process. This enables efficient stock replenishment and ensures that accurate inventory information is available to pickers.
- Technology Integration: Leverage technology to optimize the pick and pack process. Implement barcode scanning systems to ensure accurate item selection and quantity verification. Utilize warehouse management software (WMS) and order management software to automate and streamline order processing, inventory tracking, and overall logistics operations.
- Training and Standard Operating Procedures (SOPs): Invest in comprehensive training programs for pickers and packers to ensure they are familiar with the process and equipped with the necessary skills. Develop standardized operating procedures (SOPs) to establish consistency and best practices. Regularly review and update these procedures to accommodate changing business needs and improve efficiency.
- Continuous Improvement and Data Analysis: Regularly review performance metrics and analyze data related to the pick and pack process. Identify bottlenecks, error patterns, and areas for improvement. Use data-driven insights to implement process enhancements, such as optimizing picking routes, addressing common errors, and identifying opportunities for automation or technology upgrades.
Improving the Pick and Pack Process for Enhanced Customer Experience
The pick and pack process holds immense potential for businesses seeking to deliver seamless customer experiences. By understanding its intricacies and implementing the outlined strategies and best practices, companies can optimize their operations and set themselves apart from the competition.
The journey towards mastering the pick and pack process is an ongoing one, and businesses must continually adapt and improve to meet evolving customer demands and expectations. Radial takes pick and pack services to new heights to transform the customer experience. Our innovative solutions allow businesses to optimize their operations and deliver unparalleled service.
FAQs
What’s the difference between pick and pack and order fulfillment?
Pick and pack and order fulfillment are closely related concepts within the broader context of supply chain management and eCommerce operations.
Pick and pack refer specifically to the stages of the order fulfillment process that involve selecting items from inventory (picking) and packaging them for shipment (packing). It focuses on the physical tasks of gathering the ordered items, verifying quantities, and preparing them for delivery to the customer. The pick and pack process is a crucial component of order fulfillment but represents only a subset of the entire fulfillment process.
On the other hand, order fulfillment encompasses the entire process of receiving and processing customer orders, from the moment the order is placed to the final delivery of the products. It involves various stages, including order processing, inventory management, pick and pack, shipping, and delivery. Order fulfillment also encompasses other aspects such as order tracking, returns and exchanges, customer service, and post-sales support.
What’s the difference between picking and packing?
Picking and packing are distinct stages in the order fulfillment process, each with its own specific functions.
Picking refers to the process of retrieving the items or products that have been ordered by customers from the available inventory in a warehouse or storage facility. It involves pickers locating the specific products based on the order details and gathering them for further processing.
Packing orders occurs after the picking process. In the packing process, packers prepare the selected items for safe and secure shipment to the customer.
Interested in hearing more?