Streben nach kontinuierlicher Verbesserung: die 5S-Methode
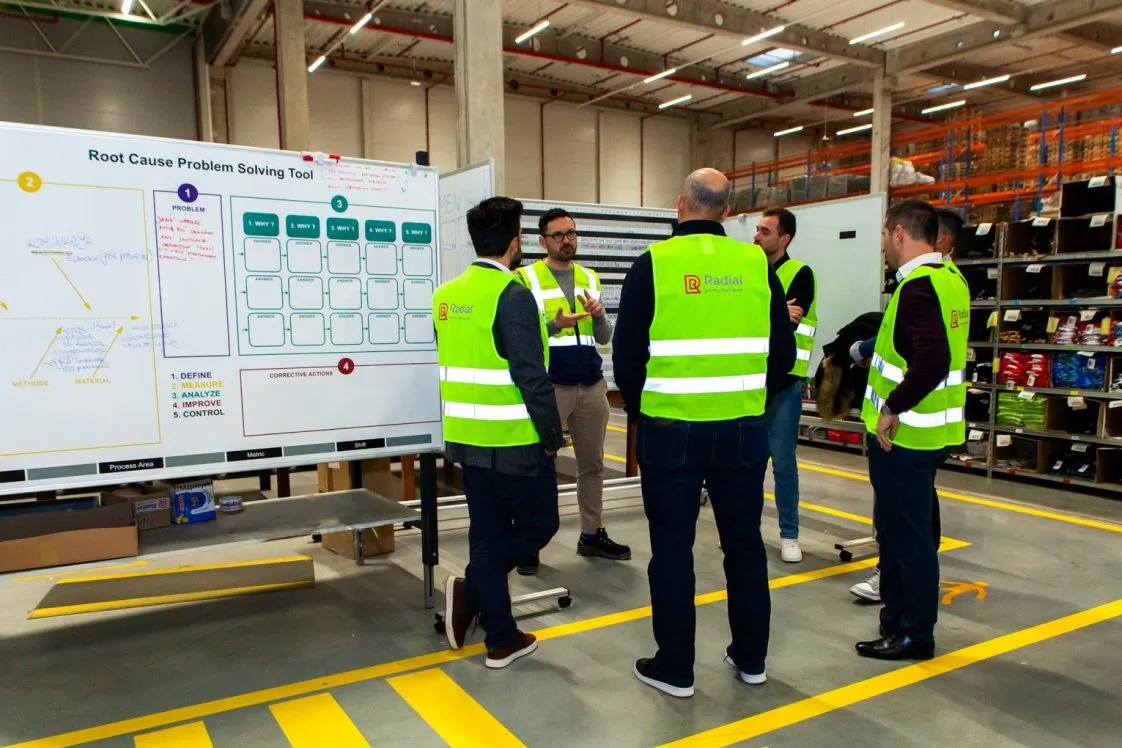
Expertenbeitrag von Karol Wojciechowski, Betriebsleiter bei Radial Europa
Die 5S-Methode bei Radial Polen
Die Einführung der 5S-Methode war eine der wirkungsvollsten Initiativen, die ich bei Radial Polen geleitet habe. Als Verantwortlicher für die Umsetzung habe ich erlebt, wie diese Methode einen Arbeitsplatz transformieren kann. Das Team in Polen war das erste, das die Methode eingeführt hat, gefolgt von Teams an anderen Standorten.
Unser Ziel ist es, die 5S-Methode auf alle unsere europäischen Einheiten auszuweiten. Bei Radial Polen wurde der Ansatz im Zuge unseres Übergangs zur Automatisierung im Dezember 2022 angepasst. Die Vorbereitungen begannen sechs Monate zuvor, um einen reibungslosen Wechsel von manuellen zu automatisierten Prozessen sicherzustellen. Heute ist die 5S-Methode ein zentraler Bestandteil unserer Abläufe.
Was ist die 5S-Methode?
Die 5S-Methode ist ein bewährtes System zur Arbeitsplatzorganisation und Effizienzsteigerung, das auf fünf japanischen Prinzipien basiert:
- Sortieren (Sort)
- Systematisieren (Set)
- Säubern (Shine)
- Standardisieren (Standardize)
- Aufrechterhalten (Sustain)
Diese Prinzipien zielen darauf ab, einen sauberen, gut organisierten und effizienten Arbeitsplatz zu schaffen, der Verschwendung minimiert, die Sicherheit erhöht und die Produktivität steigert. Ursprünglich in Japan im Rahmen der Lean Manufacturing-Philosophie entwickelt, hat sich 5S weltweit als anerkanntes Werkzeug zur Optimierung von Abläufen in Lagern und Produktionsumgebungen etabliert.
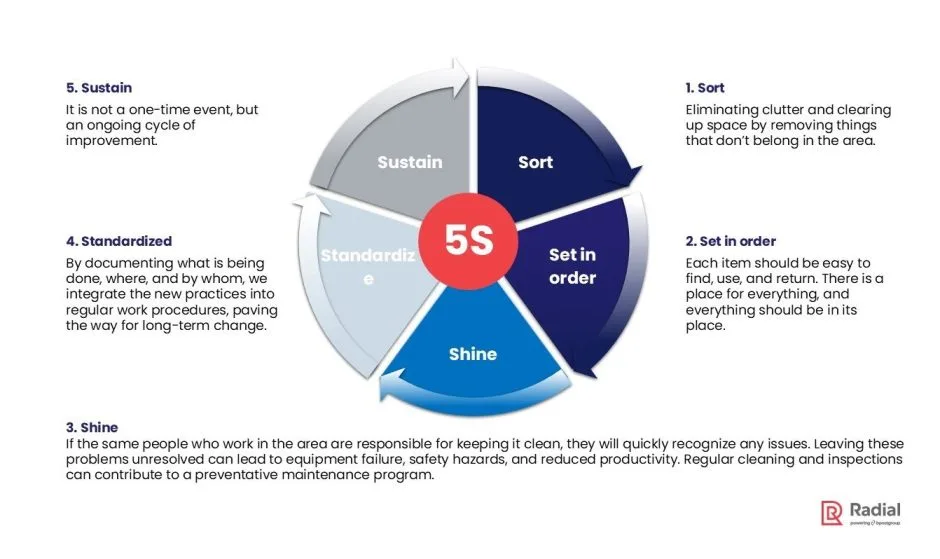
Warum nutzen wir die 5S-Methode?
Das Hauptziel der Einführung der 5S-Methode ist die Verbesserung der Sicherheit – sowohl für Waren als auch, und vor allem, für Menschen.
Durch die Optimierung der physischen Arbeitsbedingungen und die Förderung einer sicherheitsorientierten Unternehmenskultur bindet 5S Mitarbeiter aktiv ein. Es unterstützt sie dabei, Sauberkeit zu gewährleisten und eine gemeinsame Verantwortung für die Sicherheit am Arbeitsplatz zu übernehmen.
Die konsequente Einhaltung der organisatorischen Standards verändert Denkweisen, erhöht das Bewusstsein für potenzielle Gefahren und fördert präventive Maßnahmen, um diese effektiv anzugehen. Die Bedeutung von 5S zeigt sich besonders in automatisierten Lagern, wo Ordnung und Sicherheit entscheidend für den betrieblichen Erfolg sind.
Herausforderungen bei der Einführung von 5S
Die Umsetzung der 5S-Methode bei Radial Polen erforderte einen umfassenden Ansatz und einen grundlegenden Wandel in der Denkweise innerhalb der Organisation.
Die größte Herausforderung bestand darin, den Mitarbeitern zu vermitteln, dass 5S keine einmalige Initiative ist, sondern ein kontinuierlicher Prozess, der von Selbstdisziplin und der Einhaltung festgelegter Standards abhängt. Eine angemessene Schulung war entscheidend. Ohne ein klares Verständnis der 5S-Prinzipien und ihrer Vorteile hätten die Mitarbeiter die Methode möglicherweise nicht vollständig übernommen, was den Erfolg beeinträchtigt hätte.
Um dem entgegenzuwirken, führten wir Schulungen auf allen operativen Ebenen durch und organisierten Workshops, um die häufigsten Verschwendungsarten (Muda) in Prozessen aufzuzeigen.
Durch die Analyse bestehender Arbeitsabläufe aus dieser Perspektive begannen die Mitarbeiter, Verbesserungsmöglichkeiten zu erkennen. Der Fokus verlagerte sich von der Veränderung alter Gewohnheiten hin zu einer Denkweise der kontinuierlichen Verbesserung.
5S ist mehr als nur eine Abfolge von Schritten. Es ist ein Werkzeug, das die Beseitigung von Verschwendung unterstützt und eine Kultur der ständigen Weiterentwicklung in unserem Denken und Handeln fördert.
HAUPTVORTEILE DER EINFÜHRUNG DER 5S METHODE

- Verbesserte Arbeitsergonomie
- Erhöhte Sicherheitsstandards
- Beseitigung unnötiger Bewegungen (z. B. Vermeidung von Verschwendung)
- Steigerung der Arbeitsqualität
- Stabilisierung des Arbeitstempos durch Reduzierung von Ablenkungen
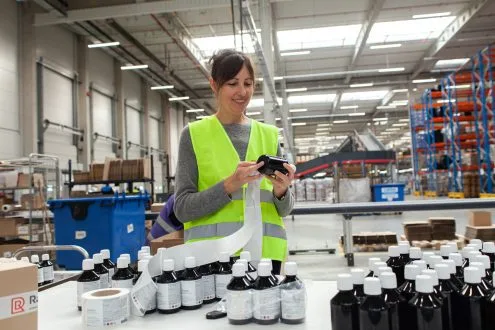
- VERBESSERTER ARBEITSABLAUF
- Zugänglichkeit und Sichtbarkeit aller Werkzeuge
- Einheitliche Ordnung und Systematik
- Sicherheit am Arbeitsplatz
- Höhere Arbeitszufriedenheit
- Starke Unternehmenskultur
- Anpassung des Arbeitsplatzes an die ausgeführten Tätigkeiten
- Stabilität der Prozesse
- Ergonomie des Arbeitsplatzes
- Freundliches Arbeitsumfeld
- Reduzierung des Verbrauchs von Werkzeugen und Materialien
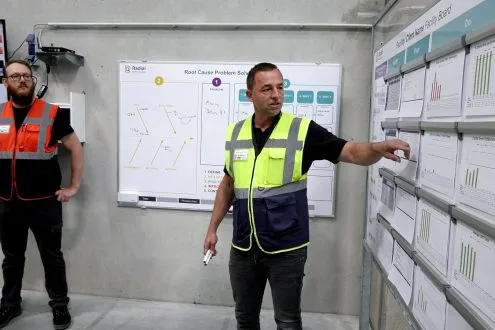
EFFEKTIVITÄT
- Standardisierung basierend auf Erfahrungen
- Anordnung der benötigten Werkzeuge in Reichweite
KONTINUIERLICHE VERBESSERUNG
- Förderung der Kommunikation mit Kolleginnen und Kollegen
- Steigerung von Wissen und Engagement
Beispiele der 5S-Methode in der Praxis
Säubern (Shine) – Den Verpackungsbereich sauber halten
In einem dynamischen Lagerumfeld, insbesondere in den Verpackungsbereichen, sammeln sich Staub, Klebeband und Verpackungsreste an den Arbeitsplätzen an. Dies kann die Qualität der Verpackung beeinträchtigen und möglicherweise die Durchlaufzeiten verlängern.
Maßnahmen:
- Einführung täglicher Reinigungsroutinen mit besonderem Fokus auf die Verpackungsbereiche, um Sauberkeit und Ordnung sicherzustellen.
- Ausstatten jedes Arbeitsplatzes mit Reinigungsmaterialien und den notwendigen Werkzeugen.
- Festlegung eines „Sauberkeitsstandards am Ende der Schicht“, bei dem jede Mitarbeitende für die Reinigung ihres Arbeitsplatzes verantwortlich ist.
- Einführung regelmäßiger Reinigungsprüfungen und Audits, um hohe Sauberkeitsstandards zu gewährleisten.
Ergebnisse:
Diese Maßnahmen führten zu einer Reduzierung von Produktschäden während der Verpackung. Zudem wurde der Kundenservice durch sauberere Verpackungen verbessert, das Wohlbefinden der Mitarbeitenden gesteigert und die Produktivität erhöht.
Standardisieren (Standardize) – Einheitliche Arbeitsabläufe einführen
In einem Lager mit mehreren Kunden führte die fehlende Standardisierung der Abläufe zu Fehlern, uneinheitlicher Verpackung und langen Durchlaufzeiten.
Maßnahmen:
- Entwicklung detaillierter Verfahren für alle Prozessschritte, einschließlich Wareneingang, Qualitätskontrolle, Produktscanning, Verpackung und Versand.
- Einführung einheitlicher Formulare und Dokumente für jede Phase, um die Nachverfolgung von Aufträgen zu erleichtern.
- Bereitstellung von Arbeitsanweisungen und Schulungen, um die Einhaltung der neuen Standards sicherzustellen.
Ergebnisse:
Die Standardisierung der Abläufe verringerte Fehler und Verzögerungen, steigerte die betriebliche Effizienz und gewährleistete eine bessere Qualitätskontrolle in jeder Phase der Auftragsabwicklung.
Aufrechterhalten (Sustain) – 5S-Standards durch das Team bewahren
Nach der Einführung der 5S-Methode in einem automatisierten Lager traten Herausforderungen bei der Einhaltung der Standards auf. Unnötige Gegenstände sammelten sich an, und die Effizienz der Prozesse nahm ab.
Maßnahmen:
- Ernennung von 5S-Verantwortlichen innerhalb des Teams, die die Einhaltung der Standards überwachen und für Ordnung im Lager sorgen.
- Organisation regelmäßiger 5S-Audits, die wöchentlich oder monatlich durchgeführt werden, um Sauberkeit, Ordnung, Raumorganisation und die Einhaltung der Abläufe zu überprüfen.
- Motivation der Mitarbeitenden zu kontinuierlicher Verbesserung durch Erinnerungssitzungen zu den 5S-Prinzipien und die Festlegung von Zielen für zukünftige Verbesserungen.
Ergebnisse:
Diese Maßnahmen stellten die langfristige Einhaltung der 5S-Standards sicher und bewahrten die hohe betriebliche Effizienz im Lager.
Die effizienteste Lagerlayoutplanung bestimmen
Ein effizientes Lagerlayout ist entscheidend, um die Kommissionierzeit zu minimieren und die Genauigkeit zu erhöhen. Der Schlüssel liegt darin, den Warenfluss zu analysieren, geeignete Lagerungsmethoden auszuwählen, moderne Technologien zu nutzen und die Prozesse kontinuierlich zu verbessern.
Lagerstrategien müssen an die spezifischen Eigenschaften der Produkte und die verfügbaren Flächen angepasst werden. Eine universelle Lösung gibt es nicht.
Um die Kommissioniereffizienz zu maximieren, müssen verschiedene Faktoren berücksichtigt werden, die wie miteinander verbundene Elemente wirken. Ein zentrales Element ist das Warehouse Management System (WMS). Bei Radial setzen wir Manhattan Active ein, das kontinuierlich um neue Funktionen erweitert wird.
Tests und fortlaufende Prozessverbesserungen stehen im Mittelpunkt der Optimierung unseres Layouts. Durch die Analyse von Daten wie Kommissionierzeiten, Auftragsgenauigkeit und Fehlerquoten identifizieren wir Verbesserungsbereiche und passen unsere Strategien entsprechend an. Dieser datenbasierte Ansatz stellt sicher, dass unser Lagerlayout stets effizient und präzise bleibt.
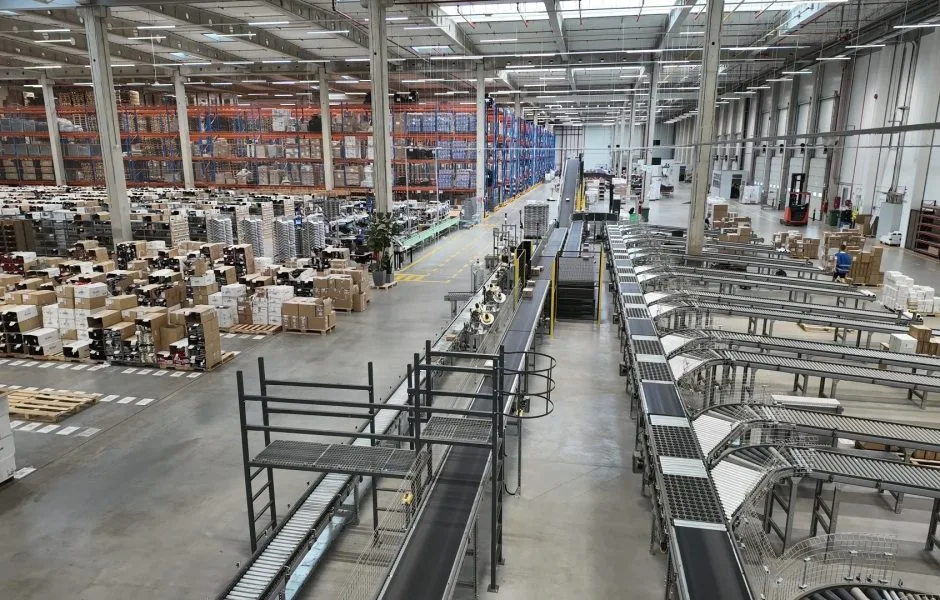
Ergebnisse und Messung der Effektivität von 5S
Die spürbaren Vorteile der Anwendung der 5S-Methode umfassen eine verbesserte Lagerorganisation, die Beseitigung unnötiger Gegenstände und eine präzisere Kennzeichnung der Lagerorte. Diese Verbesserungen führen zu einer schnelleren Produktentnahme und einer höheren Effizienz bei Be- und Entladung sowie Kommissionierung.
Wichtige Erfolgskennzahlen sind die Zeiten für die Durchführung von Lagerprozessen, wie die Dauer zur Auffindung von Waren oder zur Auftragskommissionierung. Zudem erfassen wir die Anzahl der Fehler bei der Warenplatzierung, gemessen an verarbeiteten Artikeln und Aufträgen pro Mitarbeitendem und Schicht. Diese Kennzahlen bieten Einblicke in die Auswirkungen von 5S auf die Lagerleistung und unterstützen bei der Umsetzung weiterer Optimierungen.
5S aufrechterhalten und kontinuierliche Verbesserung unterstützen
Das Engagement des Managements ist entscheidend für die langfristige Aufrechterhaltung von 5S und die Förderung einer Kultur der kontinuierlichen Verbesserung. Die Einführung von 5S geht über die Änderung des physischen Layouts hinaus; sie erfordert eine Veränderung der Denk- und Arbeitsweise des gesamten Teams.
Führungskräfte spielen eine zentrale Rolle beim Erfolg von 5S. Sie definieren die Ziele, stimmen diese mit der Unternehmensstrategie ab und priorisieren die Integration in den Arbeitsalltag. Ohne dieses Engagement könnten Mitarbeitende 5S als vorübergehende Maßnahme ansehen, nicht als dauerhaften kulturellen Wandel. Dieses Engagement ist entscheidend für die langfristige Wirksamkeit von 5S.
Kundenerlebnis
In Fulfillment-Centern sind Geschwindigkeit, Genauigkeit und die Qualität der Verpackung entscheidende Faktoren für die Kundenzufriedenheit. Durch die Anwendung der 5S-Methode haben wir die Prozesseffizienz verbessert, Fehler reduziert und die Genauigkeit bei der Auftragsabwicklung erhöht. Diese Verbesserungen tragen direkt zu einem besseren Kundenerlebnis bei.
Unser Ziel ist es, sicherzustellen, dass die Kunden mit unseren Dienstleistungen zufrieden sind und so ihr Geschäftswachstum unterstützt wird.
Empfehlung für andere Unternehmen
Die Einführung von 5S in der Lagerlogistik ist ein komplexer, aber äußerst vorteilhafter Prozess. Sie erfordert die Beteiligung des gesamten Teams, sorgfältige Planung und das Überwinden von Herausforderungen wie Widerstand gegen Veränderungen, Schulungsbedarf, Raumumorganisation und anfängliche Investitionen. Mit starker Unterstützung durch das Management kann 5S jedoch die betriebliche Effizienz erheblich steigern, die Arbeitsqualität verbessern und die Sicherheit erhöhen.
Zudem fördert 5S die Nachhaltigkeit, indem es den Raum optimiert und die Ressourcennutzung effizienter gestaltet. Ein sauberes und gut organisiertes Lager reduziert den Verbrauch von Energie, Papier, Verpackungen und anderen Ressourcen und wirkt sich positiv auf die Umwelt aus. Durch die konsequente Anwendung der 5S-Prinzipien können Unternehmen höhere Effizienz, geringere Kosten, ein besseres Arbeitsumfeld und letztlich eine verbesserte Unternehmensleistung erzielen. Daher ist 5S eine Methode, die jedes Unternehmen in der Branche in Betracht ziehen sollte.
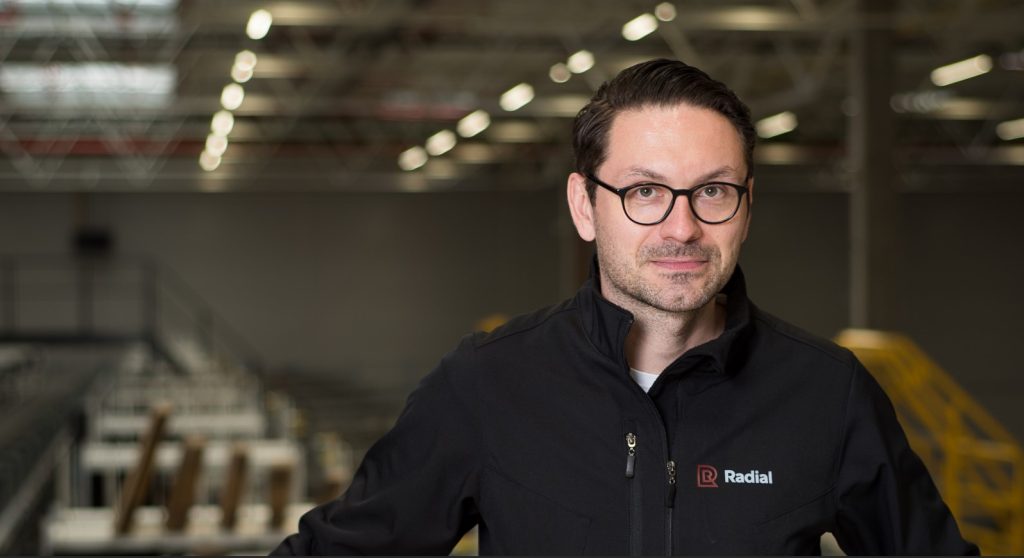
Über den Autor
Karol Wojciechowski, Betriebsleiter bei Radial Europa, ist ein erfahrener Lager- und Logistikmanager mit starkem Fokus auf Ecommerce und Lean Green Belt®-Methoden. Karol zeichnet sich durch eine hohe Organisationsfähigkeit, Prozessorientierung und Liebe zum Detail aus und hat die Fähigkeit, operative Lösungen für komplexe logistische Probleme zu liefern. Er besitzt Postgraduiertenabschlüsse in Logistikmanagement und Digital Supply Chain von der Kozminski University und der WSB University.